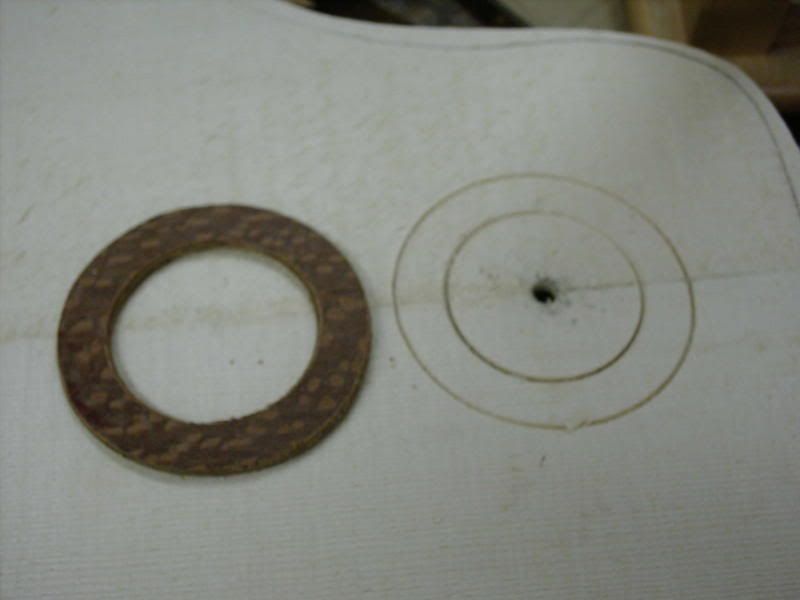
inset and with the black & white strips around the leopardwood, but before planing it all smooth

once the bracing is in, I glue in a support plate behind the soundhole. this is a Lowden thing to help support the wood around the soundhole and strengthen things .
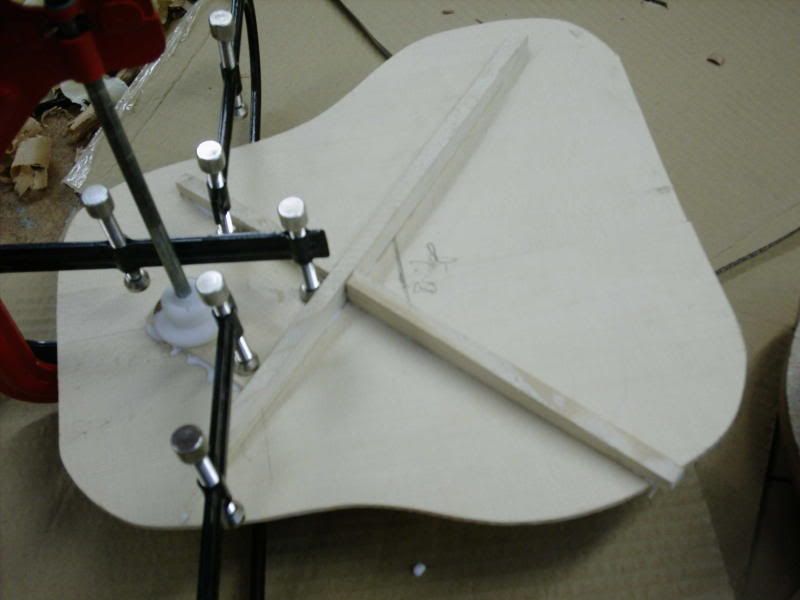
then the bridge plate to stop the ball ends of the strings chewing up the soft top wood.

And that's it for a couple of weeks as it's now the Christmas holidays and I'm locked out of school til the 5th of Jan. (yes, I KNOW it sounds a bit churlish to complain about 2 weeks of enforced holiday, but I was really "in the zone" with these two mandos!!!
still, I need to order the fretboards, tuners & tailpieces from the US and I want to let the dust settle on the Postal service before I do.
Other news is I have another commission for a similar A4 (only more fancy binding) to start when I get back, so while I'm waiting for the US order to arrive I can get it caught up to the same stage as these two.
I'm ALSO negotiating a Bouzouki based on a Sobell guitar bodied zouk for a guy locally and there is a cutaway mando on ebay at the minute so life isn't dull!!
Have a Happy Christmas everyone, and please try to remember that while a dog isn't just for Christmas, it's for life.........a hamster's for 2 years tops!!
and that, well, the whole Christmas thing is to celebrate the birth of Jesus, not the killing of a couple of million Turkeys.
God Bless, see you in JAnuary.